Focus on rearrangement of packaging at HF Jensen
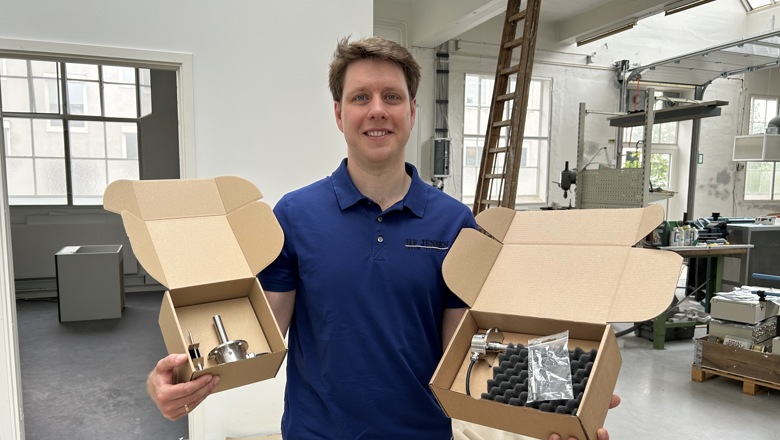
The focus on resource consumption has never been greater, and the incentives to stay in “the green lane” are only increasing. So even though the production company HF Jensen is below the minimum limit of 8 tons of packaging per year, they have signed up with VANA to get help with registration with the authorities and keep up to date with developments – for tax reasons, customer wishes and their green profile.
Companies below the minimum limit must also be registered in 2024
HF Jensen, which develops and manufactures sensors for recording pressure and distances, has an annual consumption of packaging of approx. 1-1.5 tonnes and is thus one of the approx. 33,000 companies that are below the so-called minimum limit for producer responsibility for packaging. In principle, HF Jensen can therefore continue relatively unaffected after the producer responsibility comes into force in 2025, since they will not be subject to the same financial and administrative obligations. However, this does not change the fact that they will still have statutory producer responsibility for their packaging and thus also the obligation to register in the official registers as per 31 March 2024.
Read more about registration and the reporting obligation here.
A reason to look at material consumption
HF Jensen has taken the opportunity to rethink the material consumption of their best-selling product, a sensor for marine engines. This has proved to be beneficial from both an economic and environmental point of view.
"We don't have ambitions to become a leader within the packaging field – we don't have the resources to do that. But we need to pay attention to industry tectonics if we want to stay on track. And this means, among other things, that we must have an optimised and conscious material consumption."
CEO, HF Jensen
HF Jensen has with a simple but dedicated effort, which has taken place by sparring with their supplier, managed to reduce the weight of the packaging by 28% and the volume by 42% - even at a lower price. In addition, only one material, cardboard. Previously plastics and foam was used to hold the product in place. Because of the smaller size and weight of the packaging, more sensors can now be packed in less space, the products can be shipped in smaller transport packaging, and it is easier to sort and recycle. In addition, the transport itself has also become less climate-impacting.
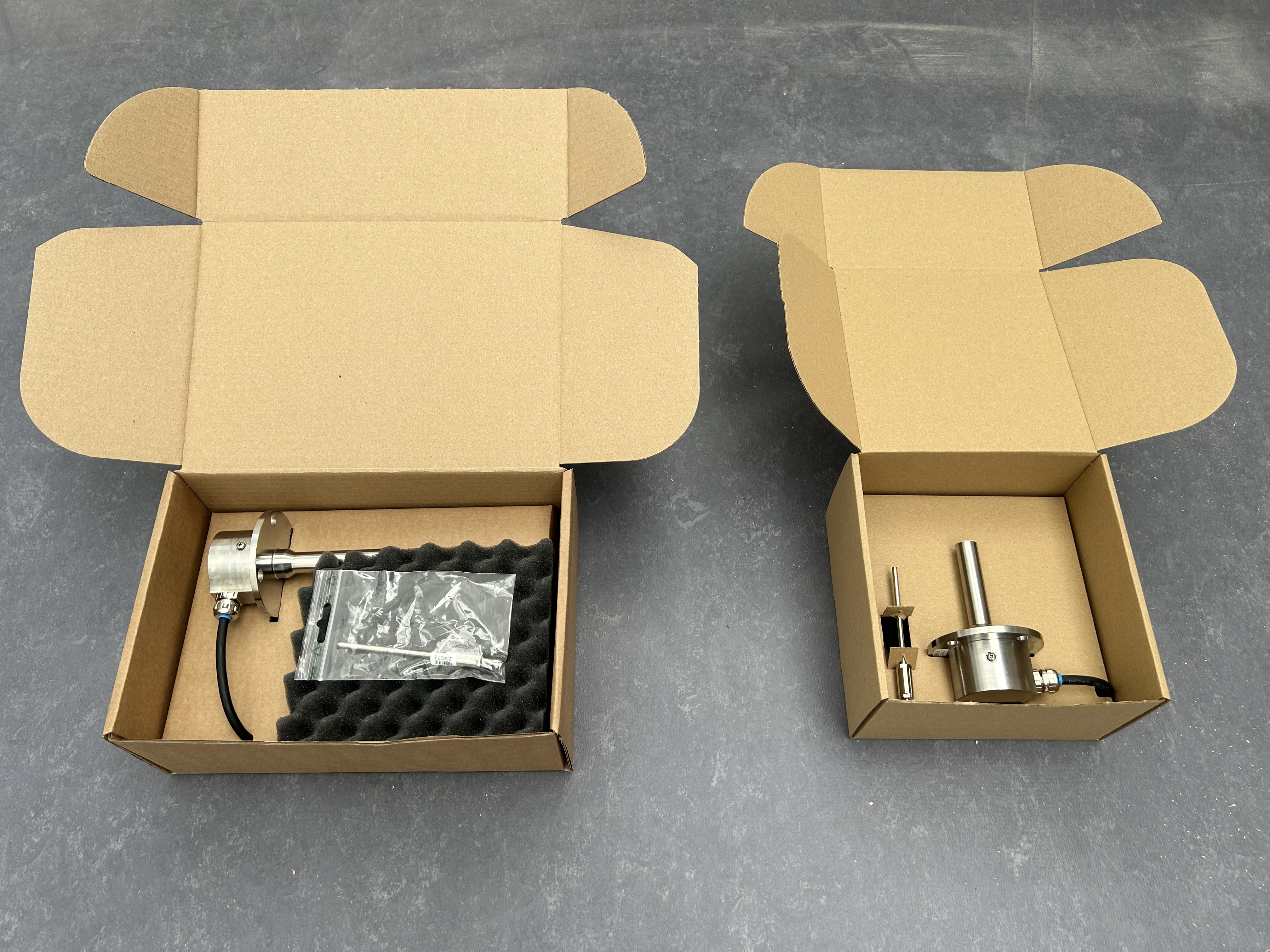
"The extended producer responsibility for packaging has been an opportunity to improve this stage of production, which can otherwise quickly be neglected in a busy everyday life – it's just cardboard. But we have received very positive reactions to the initiative, for example from our largest customer in Asia, who now needs less space to store our products. We have thus achieved some very favourable results by taking the topic seriously, and it is obvious for us to develop and evaluate our other packaging based on the requirements that come with the producer responsibility for packaging," explains Mathias Norup Panduro, who has been in charge of the process at HF Jensen.
A single, high-impact process
- We looked at our existing packaging and prioritised three obvious improvement options; three material types were used (plastics, foam, and cardboard), it was too big, and the fixation of the product was not optimal.
- The process of redesigning the packaging was simple and could be done in-house, but with important technical sparring with our supplier.
- The development consisted of measuring, shearing, cutting, and pasting with cardboard, to define the spacious conditions. So, we did a lot of physical models.
- Then we compared the solution with our transport packaging, which has some fixed dimensions, to ensure optimal compatibility and use of space.
Mathias Norup Panduro continues: "Hopefully, the producer responsibility also comes with some more tangible criteria against which we can compare our packaging. E.g., we have a number of regular customers who buy larger batches, where it will be interesting to look at whether it makes sense to recycle the packaging. Now it does not seem possible, but solutions may emerge which we can include in our production. We can measure and weigh our packaging and make sure to use FSC-labelled products, but we are not experts in recycling and circular economy. So, we hope that in the future, the conditions will promote knowledge sharing, inspiration and the long-term positive development in these areas."
VANA makes it easier to stay up-to-date.
The upcoming producer responsibility for packaging creates ripples in the water, as it also gives rise to our suppliers, who are almost all Danish, to change their solutions, which in turn can have an impact on our supply chain and daily life. As a member of VANA, we can more easily keep up to date with the developments in the industry in general, keep an eye on packaging solutions at both system and product level, and it gives us an incentive to work on a greener company profile, says Keld Lamberth, CEO of HF Jensen, about the background for joining VANA.
Read more about the benefits of being a member of VANA here.
Who is HF Jensen?
HF Jensen develops and manufactures customer-specific sensors for recording pressure and distances in close cooperation with their customers. The sensors are distinguished by providing high-precision measurements under extreme conditions such as high/low temperature and strong vibrations.
The sensors, which detect pressure, are used in everything from atomisation within the pharma industry to nuclear powerplants. Both areas place high and very specific demands on the sensors.
The distance-tracking sensors are also widely used, from cylinders in precision robots to valves in some of the world's most powerful container marine engines. Sensors for marine engines has the highest selling number, which is why HF Jensen has special focus on continuously to improve the processes around these – including the packaging.
Read more about HF Jensen here